Collision Repair Technical Training
Problem Statement
Our company is going through business expansion servicing more customers and servicing higher end vehicles with sophisticated engines and requirement for high end quality work. As a result of this, we require upgrade in skillset for technical part of daily work and increase in efficiency and quality of the work. The job market is very poor for the type of skillset we require. There is shortage in technical/high quality skillset in the market, therefore requiring us to upgrade our staff skillset to meet the growing demands in the marketplace. For today’s collision repair shop, technical training is essential to stay on top of new technologies and keeping employees at the top of their game.
Teach team to review processes, find problems, analyze, find root causes and learn to find solutions and standardize processes.
After finding root cause, team will learn to standardize the processes.
Technical Training (To individual staff in their workplace)
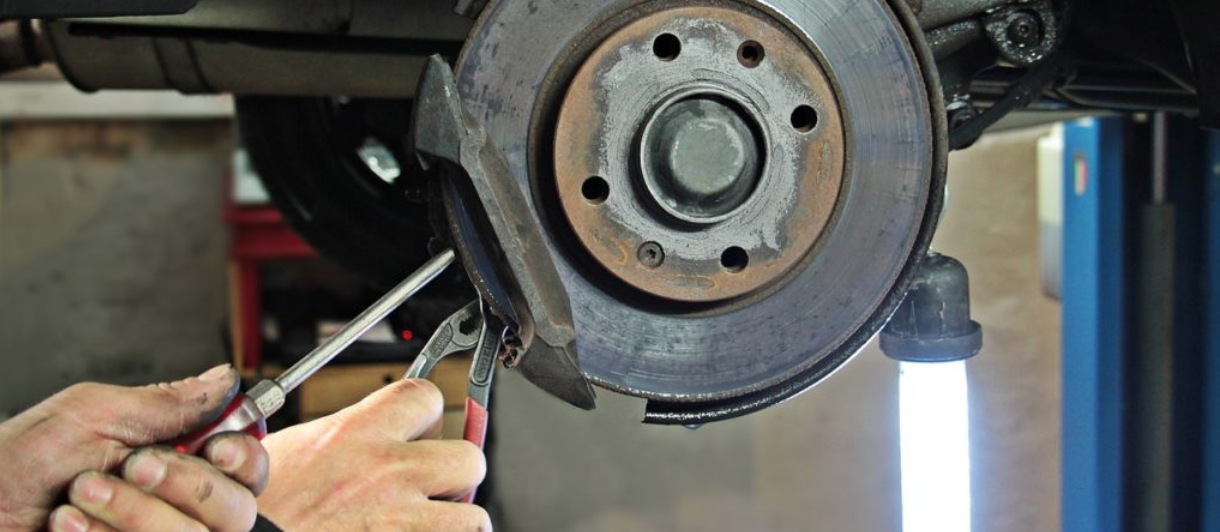
Before repair starts
- Demonstrate job file review processes;
- Explain insurance needs (including DRP and non-DRP);
- Identify express jobs using a checklist of express-related items;
- Demonstrate mapping a customer vehicle.
Communication methods
- Recognize the tools needed to conduct review and release meetings with the technicians;
- Understand the value of using and updating a computer management system;
- Identify the communication methods needed to properly share information with the team;
- Know the principles of conducting cycle time, quality, and work-in-process reviews;
- Implement awareness skills and identify roadblocks in production.
Optimizing Processes, Equipment, and Compliance
- Explain the 5S Lean Six Sigma Process and how it relates to optimized workflow;
- Inspect the building to determine maintenance issues;
- Understand parking lot, building, and vehicle security measures;
- Know the importance of equipment maintenance and maintenance schedules;
- Understand regulatory compliance issues and listing steps required to ensure the shop stays in compliance;
- Know the importance of determining proper inventory levels and storage areas.
Removing and Installing Hardware Interior Trim Training
- Identify hardware and understand correct uses;
- Understand how to work with trim and moldings.
Surface Preparation and Masking
- Finish Identification;
- Masking;
- Understanding Proper Spray Gun Technique;
- Preparing Substrates and Applying Primers;
- Making Test Panels.
Detailing
- Perform a thorough vehicle inspection and identify defects in a vehicle finish;
- Be able to remove finish defects by using the proper removal procedures;
- Understand interior and exterior detailing.
Waterborne Products, Systems, and Application
- Explain why waterborne products are used and which waterborne products are available;
- Understand the difference between waterborne and solvent-borne refinishing materials, including waterborne characteristics and benefits;
- Identify the environmental impact and reasons for converting to waterborne refinishing materials;
- Understand preparation, mixing, and application considerations;
- Explain the facility requirements for making the conversion to waterborne refinishing materials;
- Recognize proper storage and disposal procedures of waterborne materials.
Blueprinting Process and Damage Discovery
- Analyzing damaged;
- Visual control to differentiate between damage claim, old damage not part of the claim and rest of the car;
- Detail analysis of repairs;
- Listing down all damages and parts.
Color Theory, Mixing Toners, and Tinting
- Identify how tri-coat finish affects color;
- Understand how metallics and pearls affect colours;
- Recognize how a refinish color formula is chosen;
- Explain how to mix toners to make the basecoat;
- Describe how to evaluate a sprayout panel to the vehicle;
- Distinguish items and practices used for tinting;
- Describe how to tint using color plotting.
Quality Training
- Verify technicians complete quality control checklists using shop SOPs;
- Match parts invoices to the repair order invoice;
- Verify customer requests are completed;
- Compare all repair orders, sublet work, and supplements;
- Discuss the importance of quality checks after the repair;
- Examine overall repair quality using shop SOPs.
About Your Coach
Charanjit (CJ) is a passionate, results-driven professional, an enthusiastic public speaker, coach and mentor. He has 23 years of experience in transforming numerous organizations, training and coaching over 3000 individuals (on Lean Six Sigma White, Yellow, Green Belt & Lean Tools).
He supported more than 50 project teams and embedded LEAN Six Sigma in organizations varying from 100 to 7000 employees by acting as a motivator, a trainer, a coach, a mentor and a facilitator. He has coached individuals from all the sectors including healthcare, service, public service, manufacturing and construction.
He gained Lean Six Sigma knowledge while working for HONDA and since then coached or led more than 60 Lean Six Sigma project teams. CJ also led many Quality Circle teams and won best quality award from Honda, Japan.
He is a certified ADKAR Change management professional from Prosci, Lean Six Sigma Black Belt from ASQ and a Project management professional from PMI. He believes that “people are limitless” if engaged in a positive manner and can do wonders.
Check Our Other Trainings
Lean Six Sigma Trainings ⇣
Price: Contact Us
Length: 1 day
Location: GTA
Discount is Available for Organizations
Price: Contact Us
Length: 1 day
Location: GTA
Discount is Available for Organizations
Price: Contact Us
Length: 3 days
Location: GTA
Discount is Available for Organizations
Price: Contact Us
Length: 4 days (After Yellow Belt)
Location: Ontario
Discount is Available for Organizations
Price: Contact Us
Length: 8 days
Location: GTA
Discount is Available for Organizations
Project Management Trainings ⇣
Price: Contact us
Length: 0.5 day
Location: GTA
Discount is Available for Organizations
Price: Contact us
Length: 4 days
Location: GTA
Discount is Available for Organizations
Price: Contact us
Length: 1 day
Location: GTA
Discount is Available for Organizations
other⇣
Price: Contact us
Length: 1 day
Location: GTA
Discount is Available for Organizations
TECHNICAL TRAINING ⇣
Price: Contact us
Location: GTA
Discount is Available for Organizations
Previous trainees came from the following organizations
- Region of Peel
- Transport Canada
- City of Oakville
- Ontario Power Generation
- City Of Brampton
- Canada Revenue Agency
- Life Labs
- Sanofi Pasteur
- PACE Cardiology
- Meditech
- College of Family Physicians
- Akuna Health Proucts
- Hamilton Health Sciences
- UHN
- St. Joseph Healthcare
- Runnymede Healthcare
- Familycare midwives
- Coveris
- Labatt
- Campbell Soup
- Active Exhaust
- Kobay Enstel
- Cosmetica
- AYA Kitchen
- Litens Automotive
- Magna
- Dana
- Lincoln Electric
- Estee Lauder
- Thunder
- KPMG
- CBC
- D+H
- Bell
- Mississauga Bus Coach
- Club Link
- Equipment Planning Associates
- Church of God in Ontario
- American Express
- Fix Auto Collision
- WFG
- Tech Mahindra
- Metro Food Inc.
QCDMS Consultants
Formed in 2014, we believe in improving your organization's Key performance indicators: Q-Quality, C-Cost, D-Delivery, M-Morale, S-Safety.
© All Rights Reserved
Website & Video: Velbix Agency
CONTACT US
416.571.8770
inquiry@qcdms.com
QCDMS Consultants
29 Elysian Fields Circle,
Brampton, Ontario, L6Y 6E8
Canada
FOLLOW US
SPECIAL OFFER
Contact us today and get two hours of free personalized consultation and training for your company!